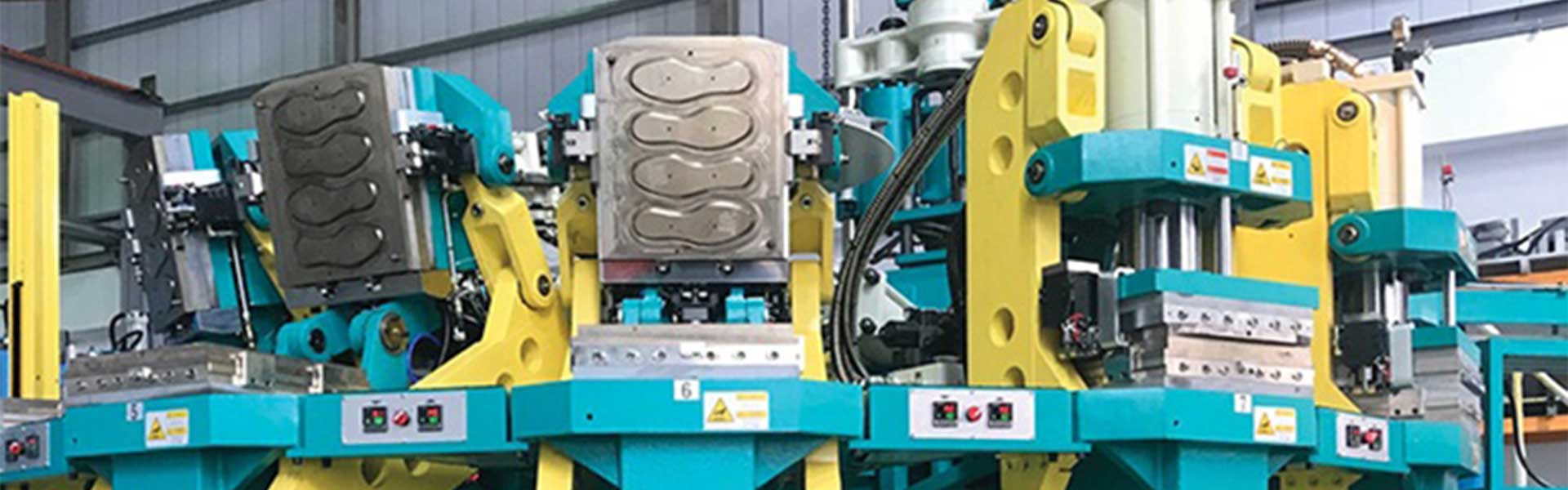
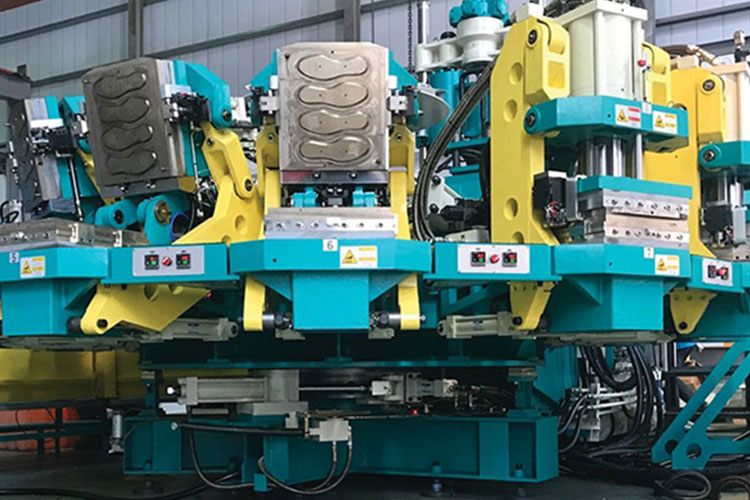
成功案例
一位客户正在寻找改进其新型轮转式注塑机的脱模工艺的方法,以降低废品率和提高生产率。
作为一家已经非常成功和成熟的制造商,该客户希望可以更好地利用自身的每一个优势。肯天与客户一起为其全新的旋转注塑工艺测试并选择理想的解决方案。
最终,肯天通过改善客户产品的粘合性,显著提高生产速度,并实现更稳定的产品质量,帮助客户实现了低于1.5%的废品率。所有产品均采用环保型水性解决方案,不仅符合法规的要求,而且对脱模剂使用量的需求更少。
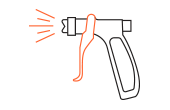
≥100%的耐久性改进 脱模剂应用频率从每3-5个周期一次缩减至每10个周期一次
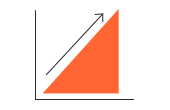
≥300%的周期改进 每两双鞋的成型时间从35-45秒缩减至10-12秒
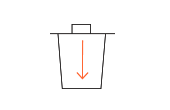
低于1.5% 肯天实现了低于1.5%的废品率
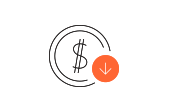
减少成本 由于更高效、更可预测的工艺,脱模剂使用量减少超过一半
过程
肯天乐于接受挑战。面对客户的高目标,我们的团队充满动力并致力于实现客户的目标。
我们发现了一些问题:
外底脱模不当
使用销钉从模具中挖出外底等不必要的手工工作
模具积垢、粘合失效和脱模不当造成的高废品率
肯天开始了一系列试验,以帮助缓解这些问题。
解决方案
肯天开发出一种新产品,可以实现更稳定的脱模,更少的转移或迁移,从而降低废品率。
肯天的影响并不止于此。全新的肯天解决方案持续时间更长,相较于之前的3-5个周期,现延长至每10个周期应用一次,从而减少了脱模剂的使用量和额外应用所需的时间。此外,脱模的方便性有助于将脱模时间从每两双鞋35-45秒缩减至10-12秒。累积效应在效率、生产率和稳定的产品质量方面产生了颠覆性影响。
手印影响
在肯天,我们为自己长期以来为可持续发展而做出的努力感到自豪。然而,客户工艺的改进才会令肯天骄傲。它超越了肯天的全球足迹;这是肯天更广泛的印记。
本案例中,肯天实现了以下目标:
提高产品质量,降低废品率
脱模剂使用量减少导致所需运输水平降低,从而减少了能源浪费
由于周期改进,整体能效水平得到提升