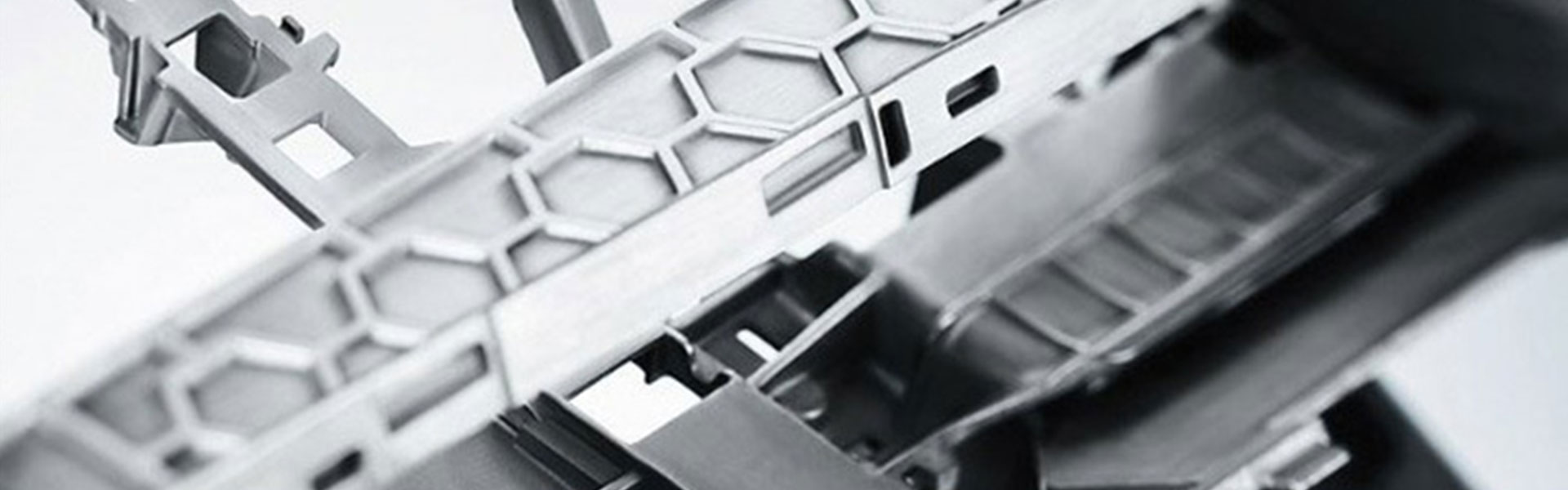
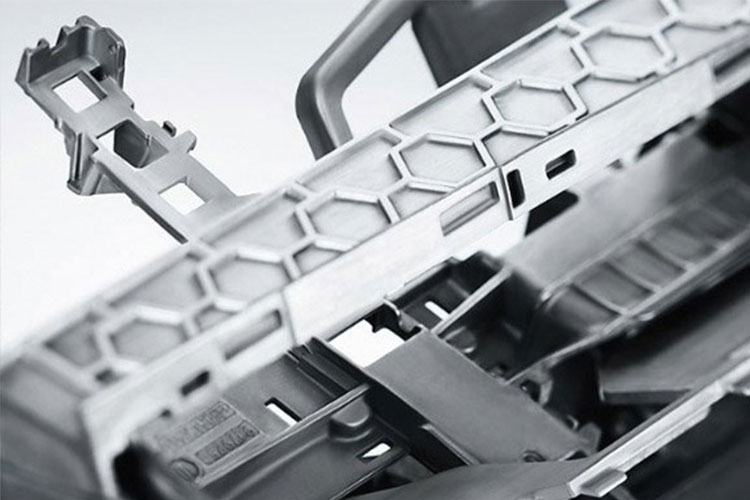
成功案例
一家欧洲压铸商专注于在面对不断增长的竞争和成本压力下增加自身的竞争力。他们在寻找一个更好的和可持续的方式去优化他们大量压铸机的生产工艺。
肯天可以通过水性的HERA™产品提供直接和广泛的影响。通过这个工艺所产生更好和节约的影响包括:
- 对于淡水的需求量减少了99%
- 由于没有额外的脱膜材料从模具流出,所以废水量减少了100%
- 消除了气泡,减少了20%的废品率
- 由于减少了热冲击显著延长了模具寿命
- 在每个生产循环中减少了20%的喷涂和吹气时间
- 显著减少了能源成本
- HERA™不含有机溶剂,因此减少了VOC的暴露
- 减少了油性材料常有的火灾风险和烟雾排放
由于非常积极的结果,这家压铸商设定了一个目标,要在三年内将其全球所有生产基地的解决方案改为由肯天提供。
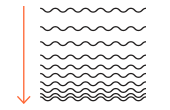
100%
100% 废水量减少
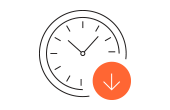
20%
20% 循环时间
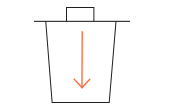
20%
20% 减少报废率
过程
通过评估和测试,我们识别到了机会:
- 脱模剂应用的周期时间相对较长
- 脱模剂应用的淡水消耗量很高
- 由于模具热量管理而过多使用脱模剂造成的高废水回收或处理量
- 在热循环中由于脱模剂对模具过分降温而对模具重新加热所产生的不必要的能源消耗
解决方案
我们应用HERA™产品解决了大部分问题。由于这种脱模剂只需要在模具表面进行轻量喷涂产生薄的涂层,所以不需要降低模具温度。这显著的减少了热冲击,延长了模具的寿命。同时这也使得生产周期显著改善,并减少了能源消耗,因此提高了盈利能力。
我们之后还安装了热过程监控系统,通过使用安装在设备上的红外相机记录实时的热力学数据。这可以进行持续的过程监控并利用HERA™不断优化。
这样的结果完全超出了客户所有的期望。这使得客户将他们所有生产工厂中的所有设备都切换成了新的脱模剂产品及相关的技术。
手印影响
在肯天,我们以可持续发展的悠久历史为荣。然而,我们对客户工艺流程的影响产生重大的影响。它超越了我们的全球足迹; 这是我们更广泛的手印。
本案例中,肯天实现了以下目标:
减少了脱模剂用量,通过模具热管理节约能源,更少的循环时间和压缩空气使用。
消除了用水脱模剂稀释和产生的废水。
由于脱模剂用量的减少运输需求,同时减少了废水运输和处理的成本。
减少废料,最终减少一切形式的浪费。
材料
废料
能源

水资源